CHEMICAL WATER PROOFING EPOXY FLOORING
Admixtures Applications
- Concrete: Admixtures are commonly used in concrete to improve workability, durability, and strength. They can also reduce water content and increase the rate of hydration.
- Mortar: Admixtures can be added to mortar to improve its workability, bond strength, and resistance to cracking.
- Grouts: Admixtures are used in grouts to improve flowability, reduce shrinkage, and enhance strength.
- Shotcrete: Admixtures are added to shotcrete to improve pumpability, reduce rebound, and increase strength.
- Self-compacting concrete: Admixtures are essential for achieving self-compacting concrete with high flowability and no need for vibration.
- Waterproofing: Admixtures can be used to make concrete and mortar more resistant to water penetration, improving their durability in wet environments.
- Corrosion inhibition: Admixtures can be used to protect steel reinforcement in concrete from corrosion, extending the service life of structures.
- Air entrainment: Admixtures are added to concrete to create air voids, which improve freeze-thaw resistance and workability.
- Accelerators and retarders: Admixtures can be used to speed up or slow down the setting time of concrete, depending on the project requirements.
- Coloring: Admixtures can be used to add pigments to concrete, allowing for a wide range of decorative options.
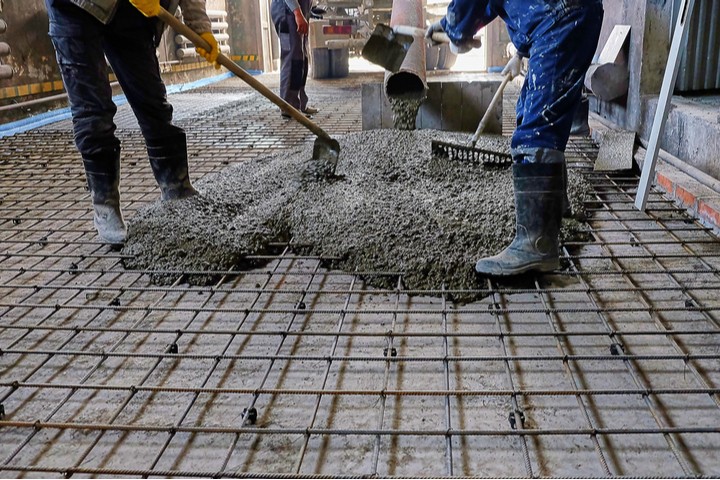
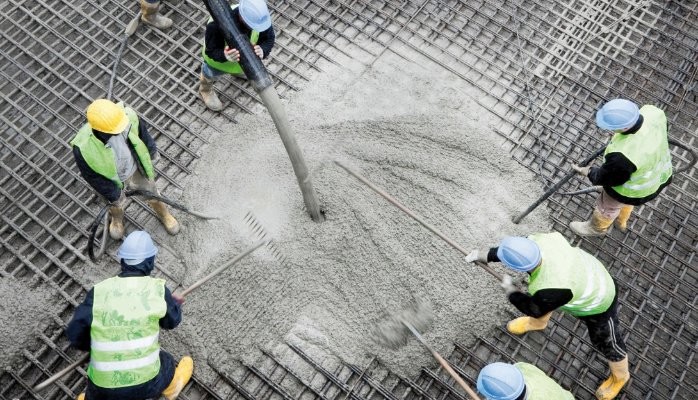
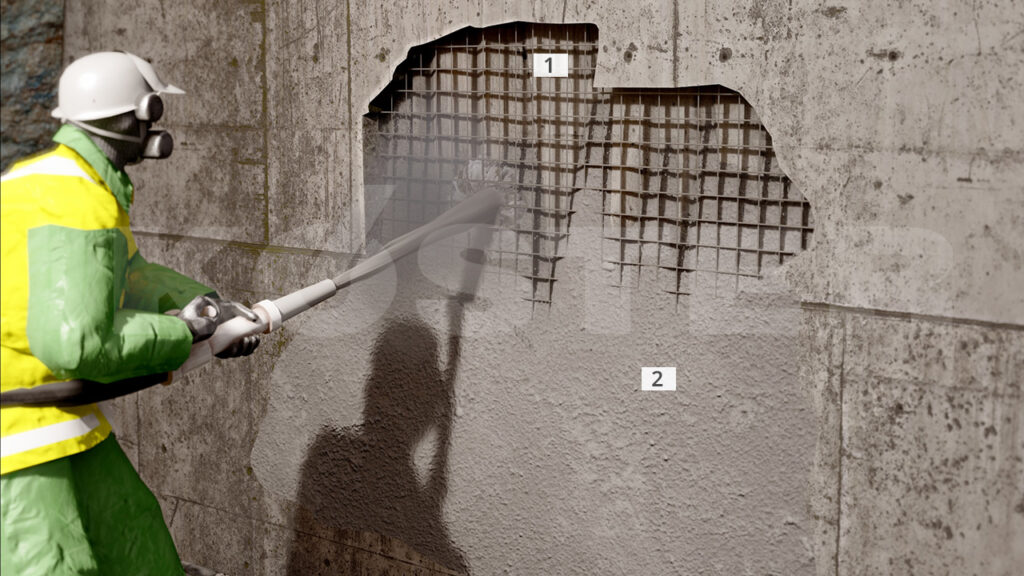
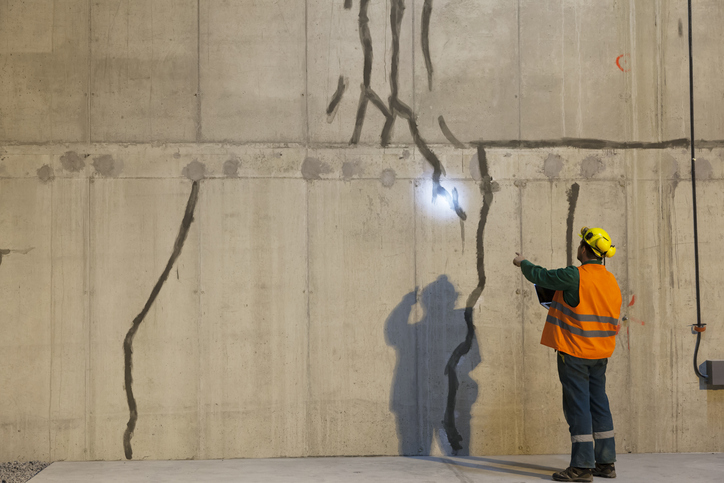
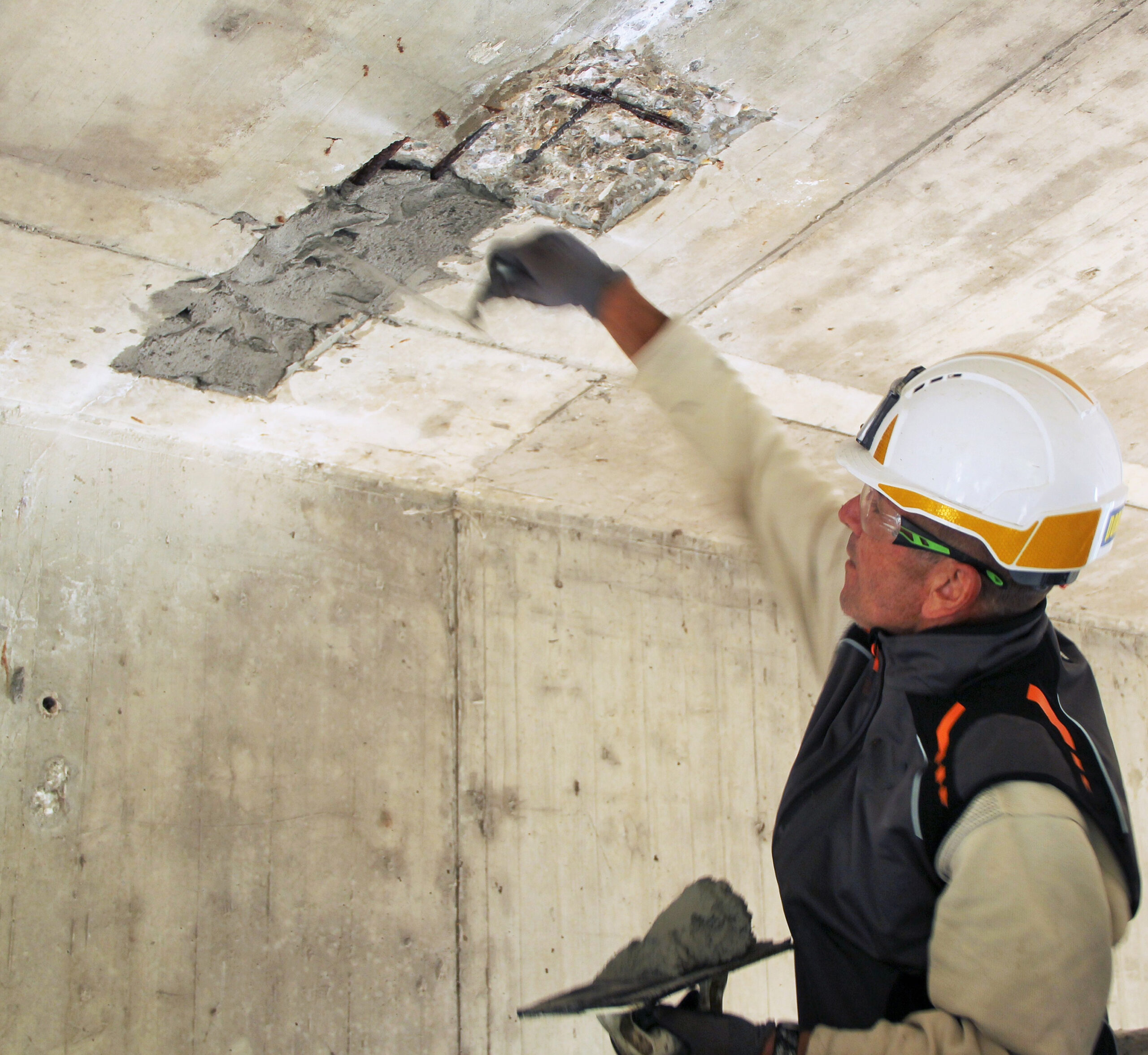
Concrete Repairs Applications
Concrete repairs are essential for maintaining the structural integrity and aesthetics of concrete structures. There are various applications for concrete repairs, including:
- Structural repairs: This involves repairing and restoring the load-bearing capacity of concrete elements such as beams, columns, and slabs that have experienced damage or deterioration due to factors like corrosion, overloading, or environmental exposure.
- Crack repairs: Concrete often develops cracks due to shrinkage, temperature changes, or structural movement. Repair methods such as epoxy injection, crack stitching, or application of sealants can be used to restore the integrity of the concrete and prevent further deterioration.
- Spall repairs: Spalling occurs when the surface of concrete breaks off, often due to corrosion of embedded steel reinforcement. Repair methods involve removing the deteriorated concrete and applying repair mortars or coatings to restore the surface.
- Joint repairs: Expansion and construction joints in concrete structures can deteriorate over time, requiring repairs to maintain their effectiveness in accommodating movement and preventing water ingress.
- Concrete overlay: Applying a new layer of concrete or a polymer-modified overlay can be used to repair and resurface deteriorated concrete surfaces, providing a fresh appearance and improved durability.
- Surface repairs: Surface defects such as scaling, pitting, or delamination can be repaired using various methods, including patching, grinding, or shot blasting to restore surface quality.
- Waterproofing repairs: Concrete structures may require repairs to address water infiltration issues, such as applying waterproofing membranes, sealants, or coatings to prevent moisture ingress and protect against corrosion.
- Cathodic protection: For reinforced concrete structures suffering from corrosion of the steel reinforcement, cathodic protection systems can be installed to mitigate further corrosion and extend the service life of the structure.
- Carbon fiber strengthening: In cases where additional structural strengthening is required, carbon fiber reinforced polymers (CFRP) can be used to provide increased load-carrying capacity and improve the performance of the repaired concrete elements.
Protective coating
A protective coating is a type of material that is applied to a surface to provide protection against environmental factors such as moisture, corrosion, abrasion, and UV radiation. These coatings can be made from a variety of materials including paint, epoxy, polyurethane, and ceramic.
Protective coatings are often used on metal, concrete, wood, and other materials to extend their lifespan and maintain their appearance. They are commonly used in industrial, automotive, marine, and construction applications.
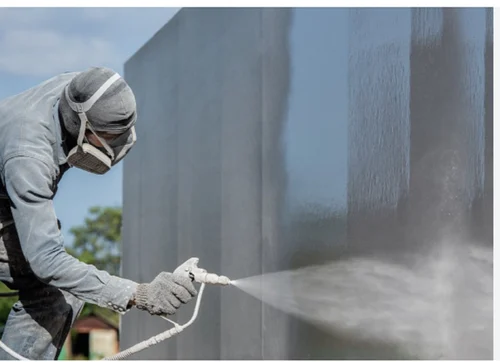
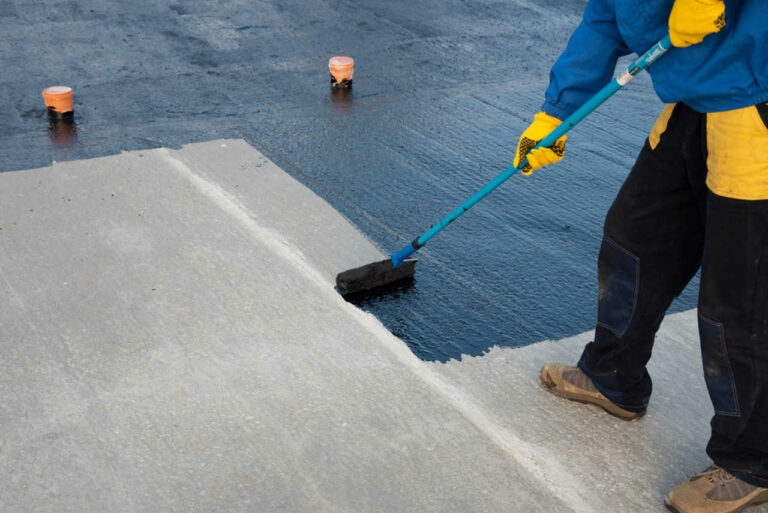
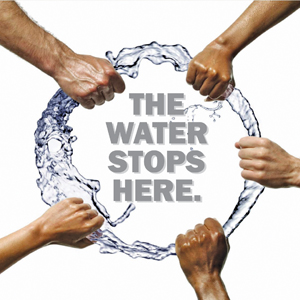
Water proofing Systems
Waterproofing systems are designed to prevent water from penetrating into a structure, such as a building, concrete structure, or any other surface. These systems are crucial in preventing water damage, mold growth, and structural deterioration. There are various types of waterproofing systems, each designed for specific applications and conditions. Some common waterproofing systems include:
- Membrane Waterproofing: This involves the application of a thin, flexible membrane to the surface to prevent water penetration. Membranes can be made of bitumen, PVC, EPDM, or other materials.
- Cementitious Waterproofing: This involves the application of cement-based coatings or additives to concrete surfaces to create a waterproof barrier.
- Liquid Waterproofing Membranes: These are applied as liquid coatings that cure to form a seamless, waterproof membrane.
- Bentonite Waterproofing: This method uses bentonite clay panels or sheets that swell when in contact with water, creating a watertight barrier.
- Crystalline Waterproofing: This system uses crystalline compounds that react with moisture to form insoluble crystals, blocking water penetration.
- Injection Waterproofing: This method involves injecting specialized materials into cracks and voids to seal them and prevent water infiltration.
Waterproofing systems are essential for basements, roofs, foundations, tunnels, and other structures to protect them from water damage and ensure their longevity. Each system has its advantages and is chosen based on the specific requirements of the project.
Sealant and adhesives
Sealants and adhesives are both used to bond materials together, but they serve different purposes.
Sealants are used to fill gaps, cracks, and joints to prevent the penetration of air, water, dust, or other substances. They are commonly used in construction, automotive, and plumbing applications to create a watertight or airtight seal. Sealants can be made from a variety of materials, including silicone, polyurethane, and acrylic.
Adhesives, on the other hand, are used to bond two or more materials together. They are commonly used in manufacturing, construction, and DIY projects to create a strong and durable bond between materials such as metal, wood, plastic, and glass. Adhesives can be made from a variety of materials, including epoxy, cyanoacrylate (super glue), and polyurethane.
Both sealants and adhesives come in a variety of forms, including liquids, pastes, tapes, and sprays, and are available for specific applications and materials. It is important to choose the right sealant or adhesive for the job to ensure a strong and long-lasting bond.
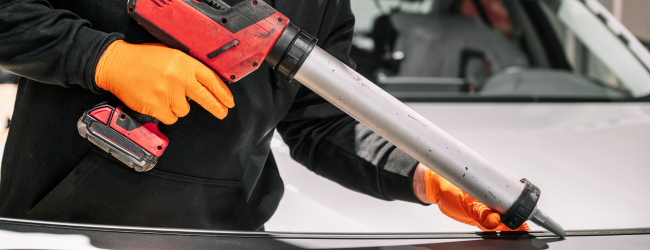

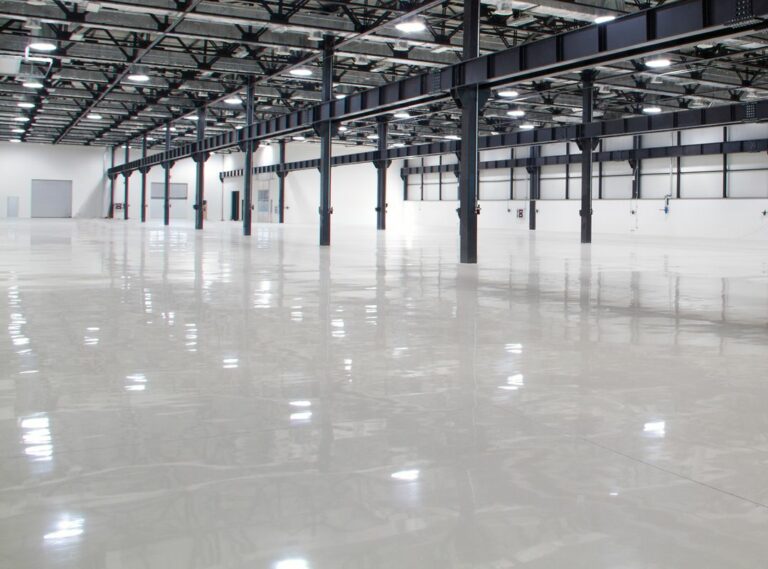
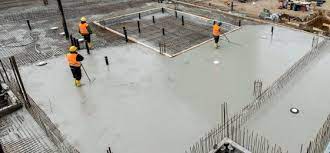
Surface treatment
Surface treatment refers to the process of modifying the surface of a material in order to improve its properties or prepare it for further processing. There are various methods of surface treatment, each serving different purposes and achieving different results. Some common methods of surface treatment include:
- Cleaning: The removal of contaminants, such as dirt, grease, or rust, from the surface of a material using methods such as solvent cleaning, abrasive blasting, or chemical cleaning.
- Coating: The application of a thin layer of material, such as paint, enamel, or metal plating, to the surface of a material to improve its appearance, protect it from corrosion, or enhance its performance.
- Surface modification: The alteration of the surface properties of a material through methods such as heat treatment, ion implantation, or plasma treatment to improve its hardness, wear resistance, or adhesion properties.
- Surface finishing: The process of refining the surface of a material to achieve a specific texture, appearance, or performance, using methods such as polishing, grinding, or shot peening.
Surface treatment is widely used in various industries, including manufacturing, automotive, aerospace, and electronics, to improve the quality, durability, and functionality of materials and components. The choice of surface treatment method depends on the specific requirements of the material and the desired outcome.